“建物の顔”といえるファサード。近年、デコラティブなデザイン、異素材の組み合わせ、特にガラスを多用するなど、前衛的・挑戦的なデザインのファサードを備えた建物が増えています。建物の付加価値のひとつとして魅力ある特徴的なデザインが求められているのです。
この潮流に対応すべく、清水建設では設計自由度を飛躍的に高めつつ、スマートな生産が可能な新構法の開発にチャレンジしています。そのひとつがこのほど発表された3次元曲面ガラススクリーン構法。複雑な形状の曲面ガラスが中空に浮いているように見せることができる画期的な構法です。この開発プロジェクトに携わったエンジニアたちに話を聞きました。
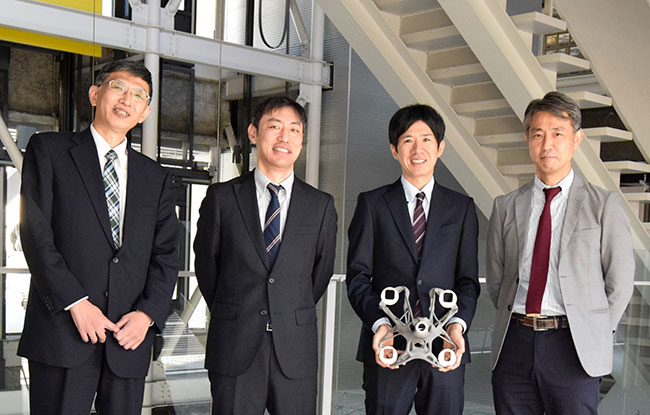
“今までに見たことのないもの”を目指して
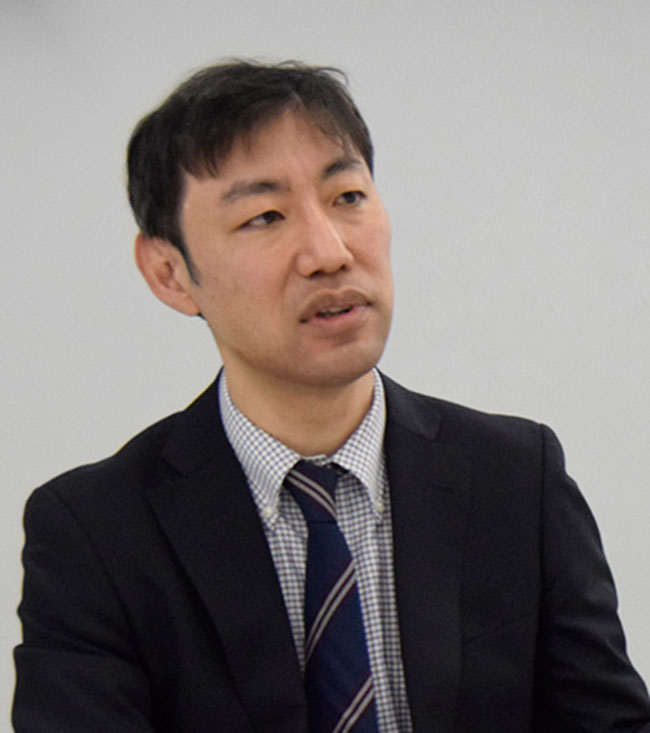
このプロジェクトは3人のエンジニアが当時新設されたひとつの部署にたまたま集結したことがきっかけでスタートしました。一人目の松尾隆士はガラスカーテンウォールや接着接合などをテーマに、建物の外装に関する研究開発を手がけてきたキャリアを持ちます。
「銀座5丁目のランドマークとなった大型商業施設の案件に関わったときに、非常に複雑な形状のガラスカーテンウォールの実現に向けて、技術支援やガラスのデザインに携わりました」(松尾)
このとき、松尾はこうした建築ニーズは今後どんどん増えるだろうと予感したといいます。
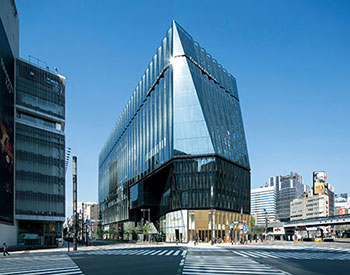
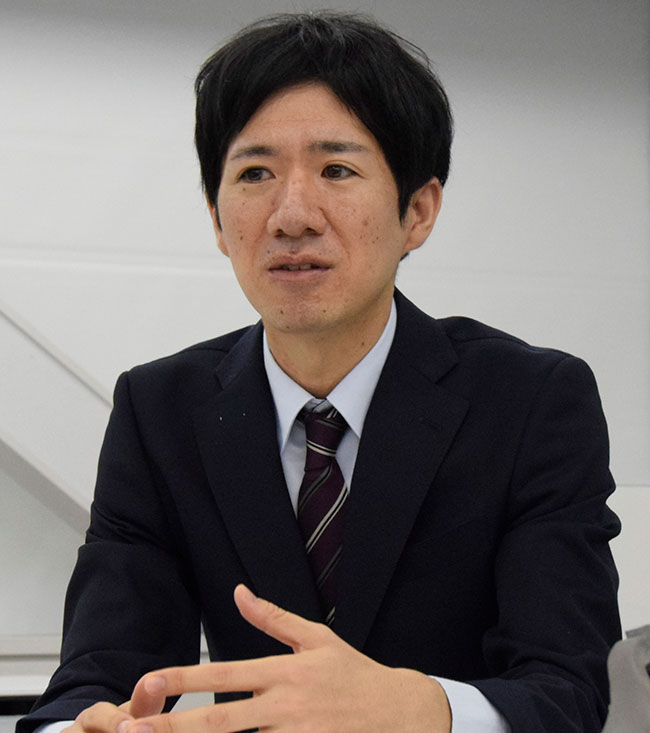
二人目の佐川隆之は、建物の構造、特に異素材を組み合わせたハイブリッド系の構法や、地震、津波、降雪といった自然災害が建物の構造に及ぼす影響とその対策についての研究開発を担当してきた気鋭のエンジニア。
「このプロジェクトではガラスと建物をつなぐ支持金物の開発を担当しました。博士論文で研究していたテーマがRC柱とS(鉄骨)梁を組み合わせたハイブリッド構造の接合部についてで、今回の開発に役立ってくれました」(佐川)
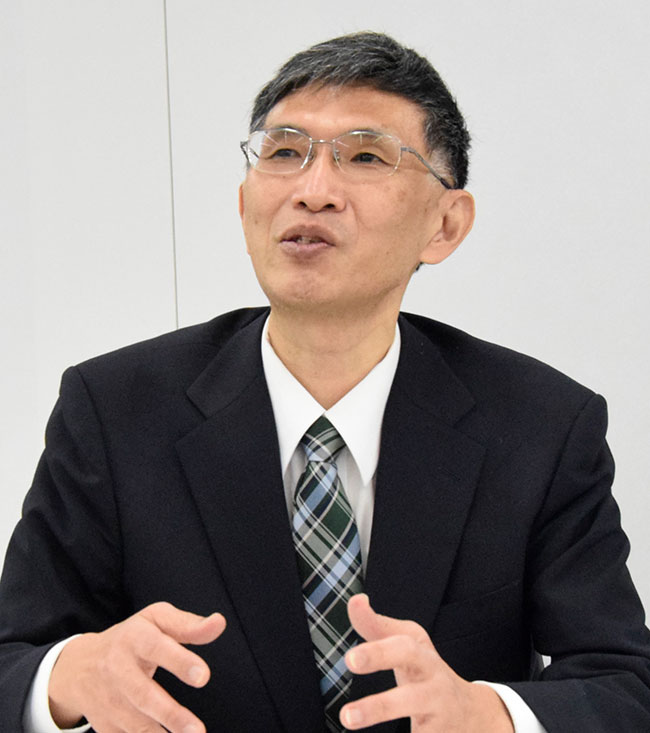
そしてもうひとり、兼光知巳は入社以来30年以上にわたって構造体、それも一風変わった形状の構造体の研究を続けてきたベテランです。
「2011年頃、シンガポールのオーチャードロードという、外装のガラスがそのまま構造体となるような建物に関わったときに、これはおもしろいなと思いました。今後はこうした建物がきっと増えていくに違いないと考えていたのですが、最近になって海外でそんな建物が次々に出てきたのです。これは本格的に研究開発していこうということになりました」(兼光)
兼光と松尾が中心となり、このトピックについて議論を重ねているうちに、少しずつ目指すべき技術のアウトラインが固まっていき、2019年4月にプロジェクトはスタートを切りました。
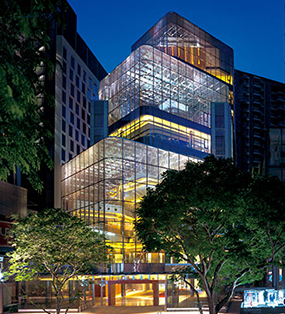
先端分野の技術を建築に適用
3Dガラススクリーン構法には大きく4つの革新的な技術が適用されています。
(1)3次元曲面ガラスの実現
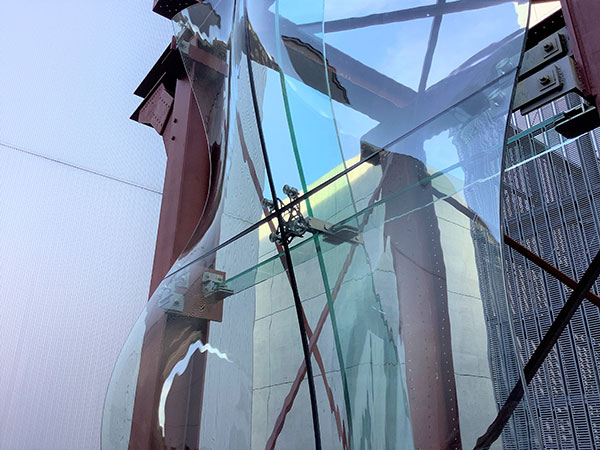
従来も曲面ガラスはありましたが、一片が1mを超えるサイズで、三次元でうねるような自由曲面を描き、さらに強度確保のために2枚の合せガラスになっているというのも前例がないものです。
「今回は実験用モックアップということで製造限界まで曲げてみました。しかも2枚を合わせたときに一体になるようにするためには、製作精度のわずかな誤差も許されません。開発当初は何度も失敗しましたね」(松尾)
従来の強化ガラスは熱処理を加えて作られますが、今回のガラスには硝酸カリウム溶液による化学強化処理が採用されました。これを建物の外装用途に用いるのもはじめての試みです。
「熱処理をすると加工時にゆがみが発生し、2枚を合わせるのはより困難です。その意味でも化学強化処理が現時点でのベストな選択でした」(松尾)
(2)接着接合の採用
従来のガラスファザードはガラスに穴を開けて支持金物を通し、支柱に接合する構造で、それぞれに製造誤差や施工誤差を吸収できる『遊び』として調整代(しろ)を設けることができます。これに対し、今回はガラスの接合に接着剤を採用しています。
「3Dガラスを精度良く取り付けるのは予想以上に困難でした。接着剤を利用する方法なら微妙な調整も容易になります。この接着剤は紫外線に対して耐性が高く、試験結果では少なくとも30〜40年ほどの耐久性を備えています」(松尾)
(3)ジェネレーティブデザイン、3Dプリンターによる支持金物製作
3Dガラスが取り付く支持金物はジェネレーティブデザインの手法で設計され、さらに金属3Dプリンターによって作られています。ジェネレーティブデザインとは、設計者がコンピュータに設計要件として一定の情報を入力し、最適な製品設計を生成(=ジェネレート)する先進的なテクノロジー。
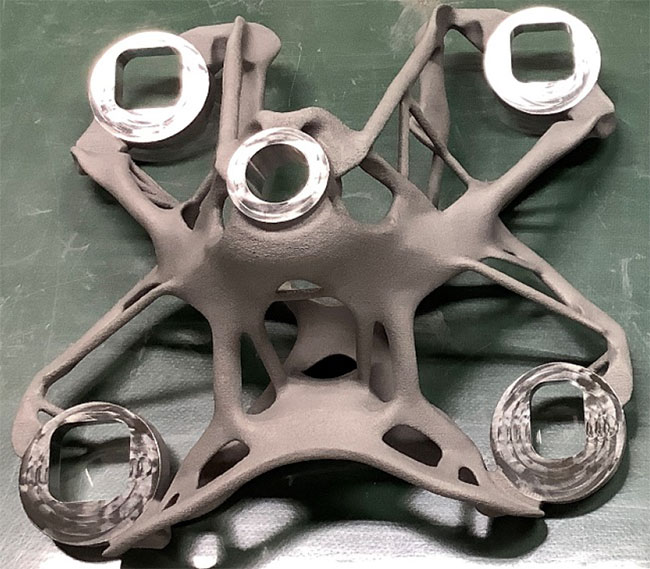
「自重に加え、風圧や地震の揺れに対する変形の追従性、さらに施工性も考慮して、構造的にもっとも合理的な形状をコンピュータ上で作りました。今までにない新しい構法に向けたものなので、想像の範囲内に収まらない見た目のインパクトという点も意識しました」(佐川)
2020年9月の検討開始から2021年2月の最終案決定まで、荷重条件や固定領域などを試行錯誤して、およそ50案のパターンを検討したといいます。
「デザイン案は有限要素法を用いた数値解析も実施するなど、入念に性能をチェックしています。出来上がったものをカーテンウォールメーカーのエンジニアに紹介したら非常に興味を持ってもらえました。このときには手ごたえを感じましたね」と笑顔を見せる佐川。
(4)デジタル活用による性能検証と施工管理技術
実用化に欠かせない性能の検証と施工管理技術については、シミュレーションをフル活用した性能検証、3Dスキャナによる精度計測など、最新の知見と技術を採用しています。
「たとえばガラスの強度計算は従来の手法では追いつきませんし、フラットなガラスとは比較できないほど施工も難しい。完成したガラスをさらに3Dスキャナで測定してデータ化し、シミュレーションを重ねて強度確認をしました」(松尾)
プロジェクトを指揮した兼光は次のように話します。
「3Dガラス、接着接合、支持金物の製作法、デジタルによる検証と、いずれも航空宇宙などの先端分野では要素技術としては確立されてはいるものの、建築分野、ことに構造領域への適用は世界でも前例がないものばかりです。それぞれを我々の目標に合わせるために、各メンバーが苦労して確立させた技術です」(兼光)
建物の構造の概念を一新するかもしれない
さまざまな困難を乗り越え、多様な技術を組み合わせて開発された3Dガラススクリーン。部材単位の性能検証は個々に実施されていましたが、すべてを組み合わせたユニットとしての性能を確認するために、2021年10月、実大実験による性能検証が行われました。モックアップをそのまま試験体として、風圧や地震を想定した負荷を与えた結果、東京都心の低層の建築には十分に使える性能を確保していることが実証されました。
「ガラスにせよ、支持金物にせよ、デザイン的にギリギリのところで設計したものだったので、本当に風や揺れに耐えられるのか、ハラハラしながら立ち会っていました。きちんと性能が出て、本当にホッとしたことを覚えています」と松尾がいえば、「支持金物が壊れたらガラスも飛んでしまうわけですから、祈るような思いで見ていました」と佐川も振り返ります。
今後、この構法は実案件への適用というフェーズに移行していくわけですが、ここで大きな期待を寄せられているのが、ファサードメーカーのエンジニアをしていた経歴を持つ安田辰雄。彼は実用化、現場適用に向けた動きを担っていくエンジニアのひとりです。
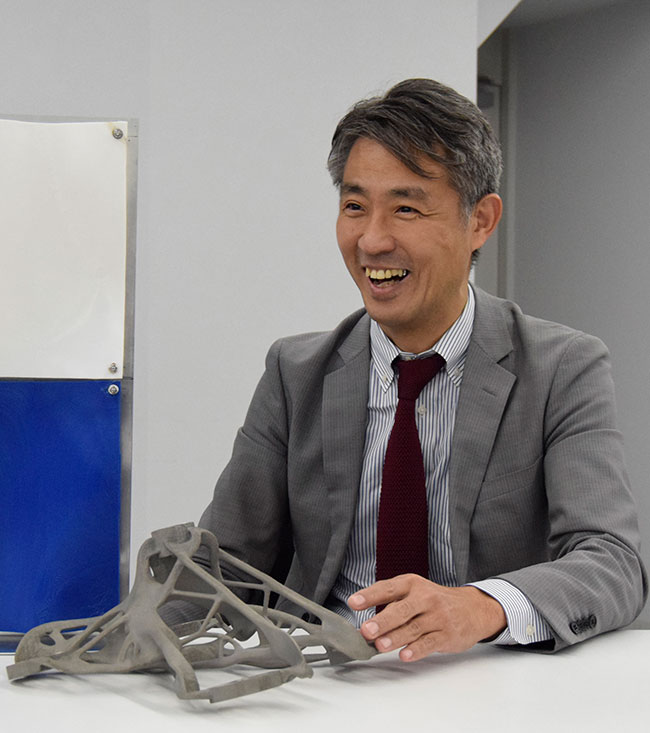
「このプロジェクトで開発された技術は、ひとつひとつが非常に大きなポテンシャルを備えています。たとえば従来の熱強化ガラスはさまざまな要因で自然に爆裂してしまうことがあるのですが、化学強化ガラスはそうしたことがありません。また、支持金物に適用されたジェネレーティブデザインは力の伝達を可視化したもので、押出材を加工して作る金物に対して、制作過程で一切無駄が出ない。これはSDGsのコンセプトにもフィットします。接着構法も今ある機械的な接合方法に変わって主流になりうる可能性を秘めています。こうした最先端の技術開発に関わることができて、本当に楽しいです」(安田)
この技術は今後の建築のあり方を変えていくかもしれないと兼光は話します。
「外装の3D曲面が当たり前になれば、構造体も複雑な3D形状で構成できるようになるでしょう。現在の建物の屋根、外装、柱、梁などといった概念自体が根底から変わっていくかもしれません。そんな未来のきっかけにこの技術がなったとしたらうれしいですね」(兼光)